
News
Search all news
Aurizon drives down emissions with rail-based logistics solution for BHP Copper South Australia
Australia’s largest rail freight business Aurizon has been selected to deliver an integrated rail, road and port logistics solution for BHP’s globally significant Copper South Australia province.
Latest news
Aurizon’s Community Giving Fund: building stronger communities together
24 Jun 2025

Aurizon drives down emissions with rail-based logistics solution for BHP Copper South Australia
16 Jun 2025
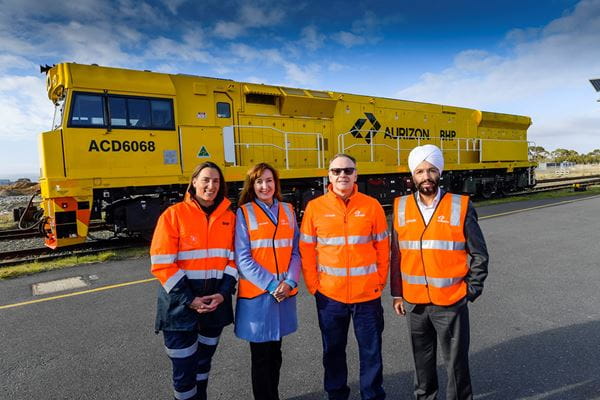
Empower your community: apply for Aurizon's Community Giving Fund today
17 Mar 2025
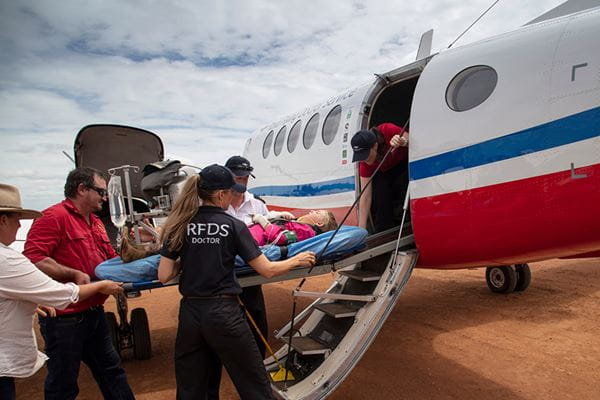
ANL and Aurizon partner on Landbridging through Darwin
17 Feb 2025
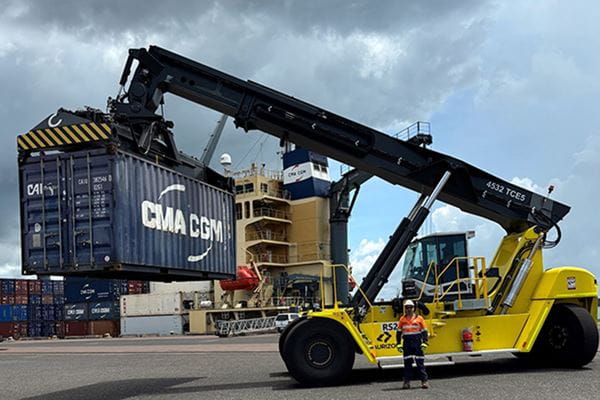
Aurizon's Community Giving Fund: Supporting local initiatives
17 Dec 2024
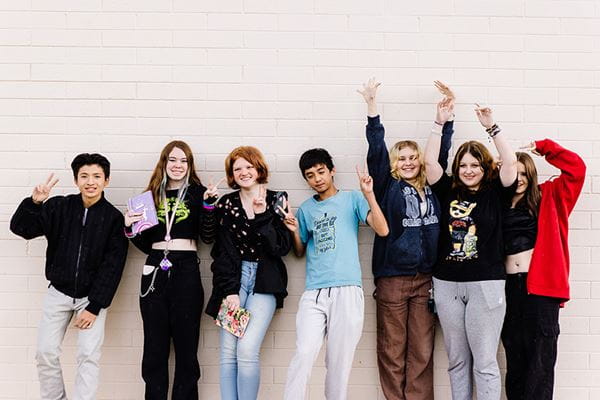
Approval for acquisition of Flinders Logistics
28 Nov 2024

First train hits the tracks for Gold Valley
04 Oct 2024
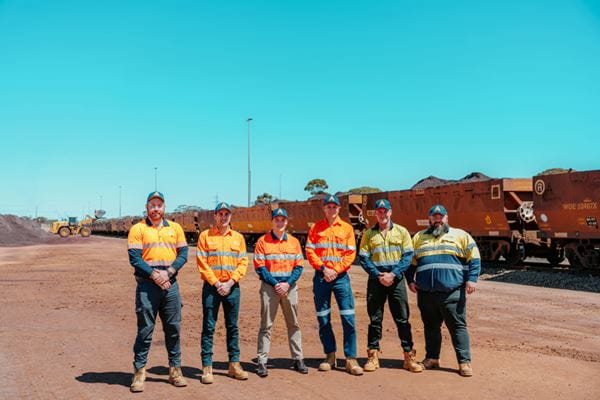
What could you do with a cash grant from Aurizon’s Community Giving Fund?
16 Sep 2024
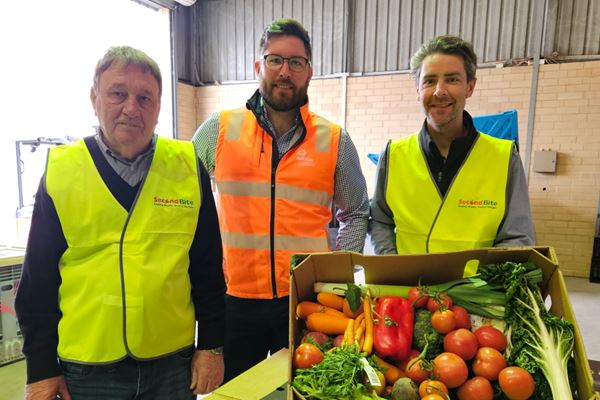
Aurizon and Mackay Council partner on native reforestation project
04 Sep 2024
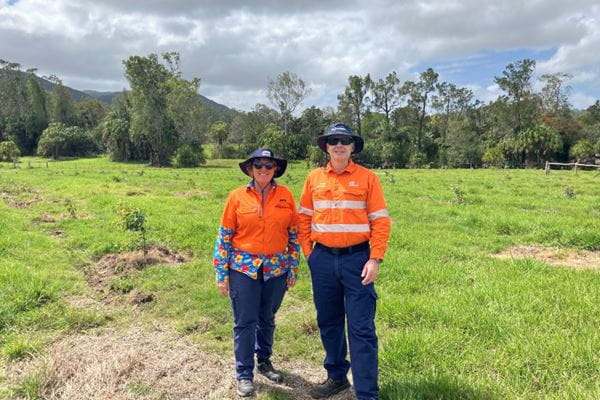
Stories
Anzac Day - Honouring 110 Years of Sacrifice and Service
23 Apr 2025
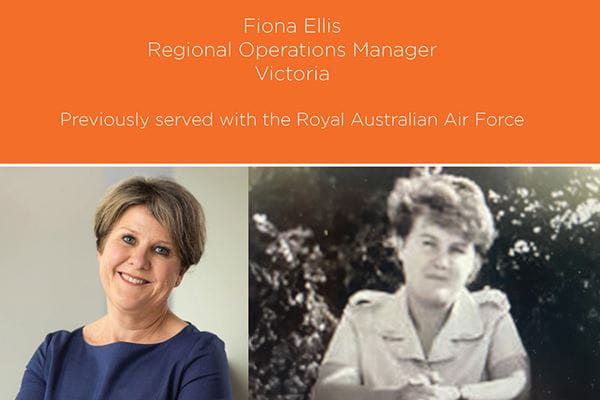
Train driver Lauren Blake shares her story as part of National Rail Safety Week
09 Aug 2024
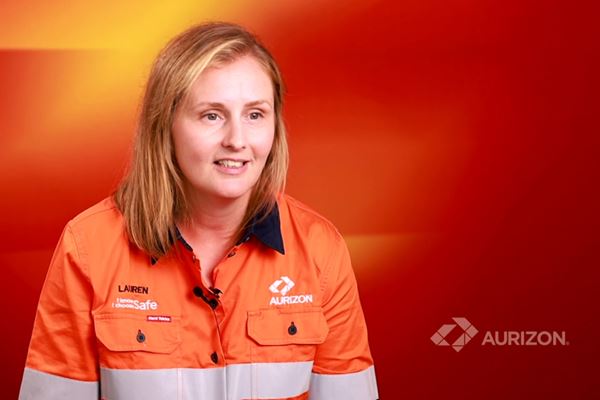
Train driver Hamish Withington shares his story as part of National Rail Safety Week
05 Aug 2024
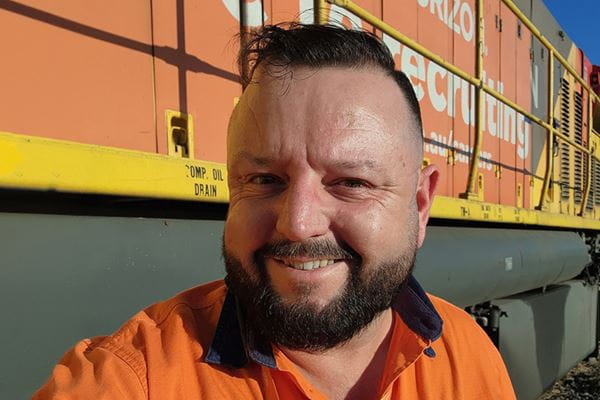
Celebrating our First Nations people
27 May 2024
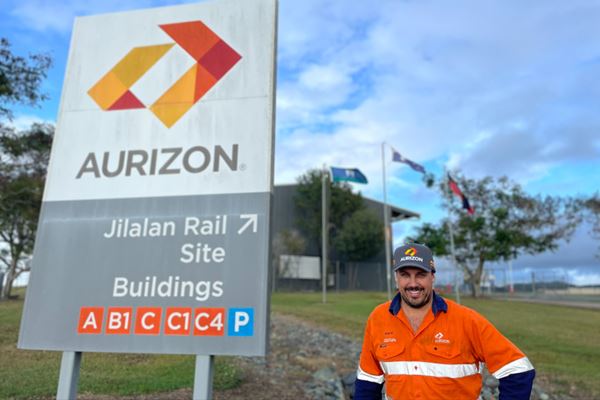
Anzac Day - A day of reflection and gratitude for our veterans
24 Apr 2024
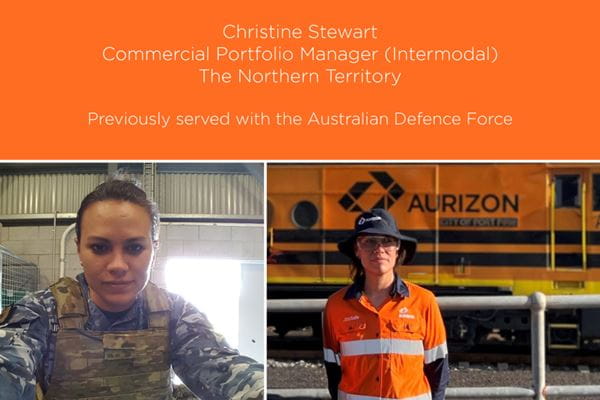
Leading the way in technological innovation
08 Mar 2024
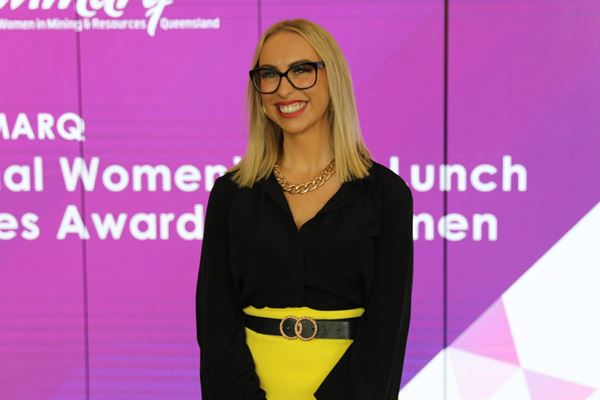
Celebrating NAIDOC Week with Jacob White
04 Jul 2023
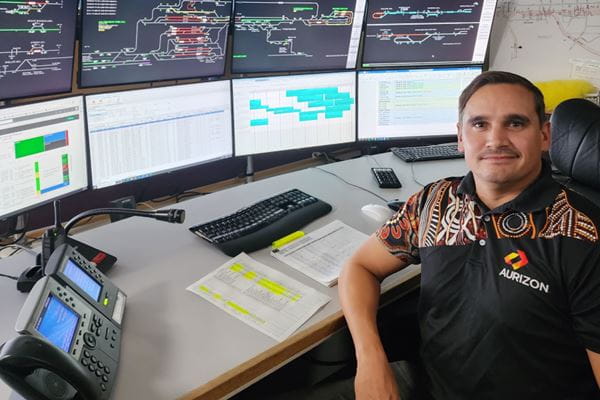
Aurizon’s Caitlyn Gallagher shares her story as part of National Reconciliation Week
01 Jun 2023
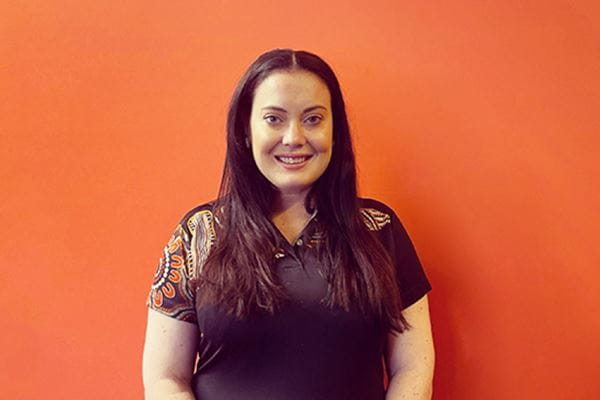
Commemorating our veterans on Anzac Day
24 Apr 2023
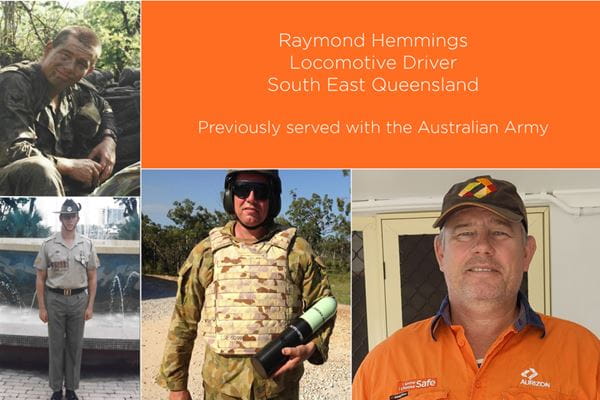